Why Choose Carpet
Our goal is to provide you with soft, welcoming carpet that will meet your needs while beautifying your home. We are committed to providing you with the very best in carpet products while helping you choose the flooring solution best suited for your home and your family. Learn more about the features and benefits of carpet now.
Carpet has been a beloved flooring solution since ancient times. First gaining popularity in the sixteenth century, carpet first came to Europe with merchants, adventurers, and explorers who had obtained beautiful, exotic textiles from the East. Before long, awareness and demand for these textiles grew, eventually reaching the United States. Today, carpet is a fundamental part of homes and businesses all around the world.
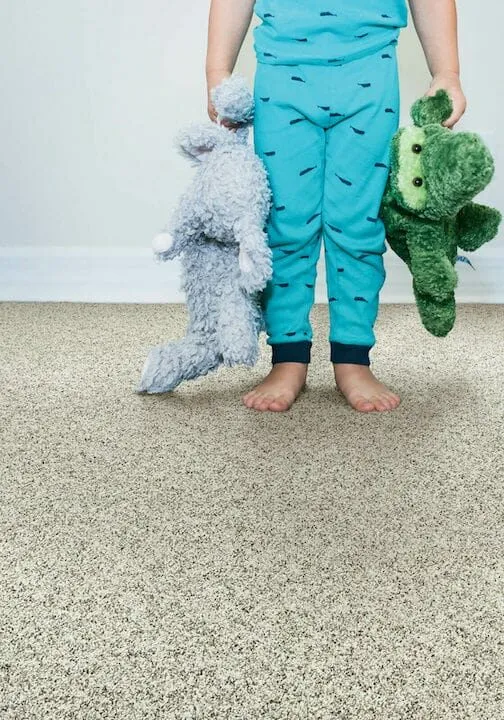
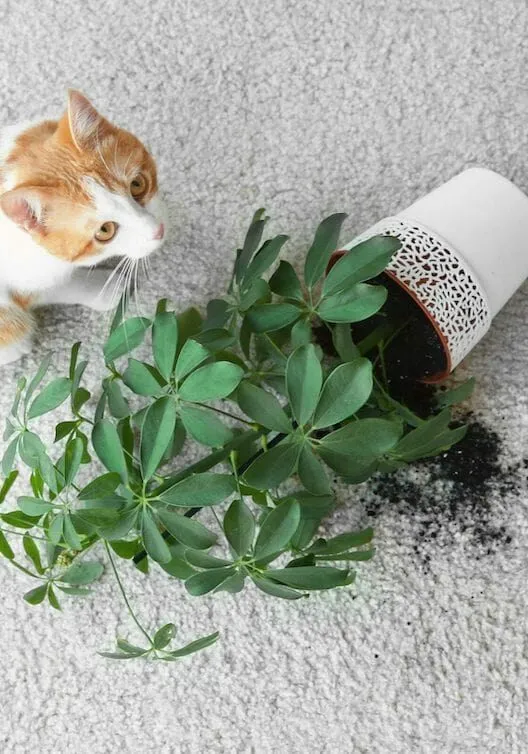
Before You Buy Carpet
Choosing the best carpet is about knowing the right combination of characteristics, aesthetics, performance, and budget to best meet the needs of your lifestyle. Whether you want a luxurious carpet in your bedroom, high-performance carpeting in your family room, or you need an affordable carpet, we have the best carpet choices in the area. We want you to know all the important facts about carpet specifics and characteristics. The more you know, the better able you will be to make a smarter purchase decision.
Carpet Colors
Carpet covers a large area of any room, so it is important to keep some basic rules in mind when selecting your carpet. Once a carpet is installed, it will often look lighter than the sample. Lighter color carpet will visually expand the size of the room, while darker carpet will create a more intimate feeling. Neutral colors are the best choice for frequently changing decorating schemes or if you are trying to incorporate a large amount of existing furniture. A neutral color is also a good idea if the home will be resold at any time. Whatever you prefer, we have the most popular carpet styles currently available.
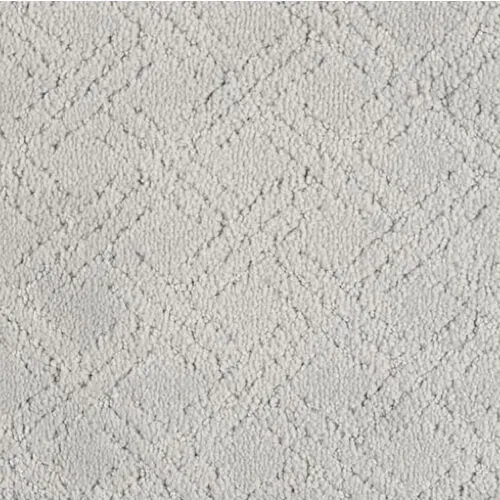
Grey Carpet
The color grey is a much-loved neutral tone, and grey carpeting can bring a timeless quality to your room. It's a popular decorating trend that will never feel dated. You can support any other color in your design scheme when you use grey carpeting, but blue, gold, cream, and dark red are classic combinations.
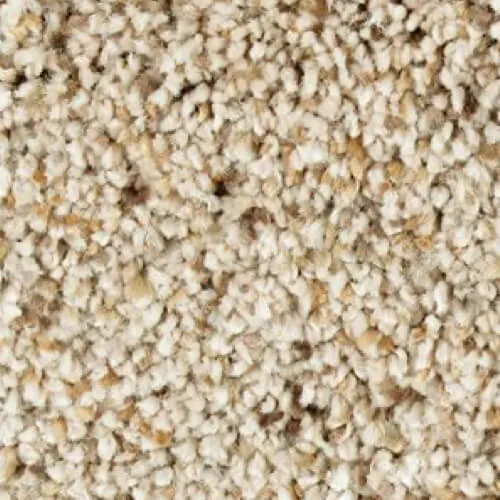
Beige Carpet
Like grey, beige carpeting is a classic option that will support almost any color design scheme. From the lightest taupe to a rich tan and everything in between, beige carpeting looks sophisticated in a living room and peaceful in the bedroom. It can make a statement in a hallway or entryway too.
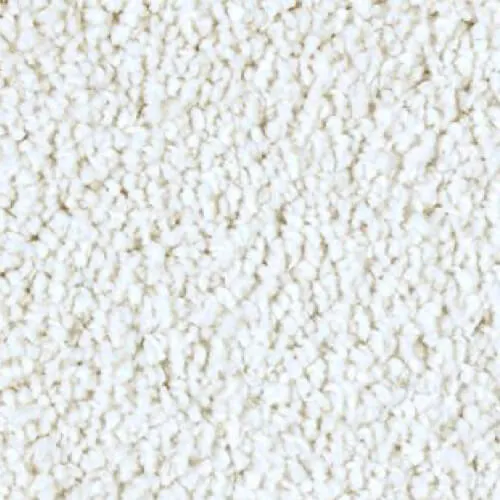
White Carpet
White carpeting is a neutral yet dramatic choice. It lends an elegant layer to the living room or bedroom. And while it might not be a practical choice for a family room or kids' bedroom, it can really shine in other areas throughout your home!
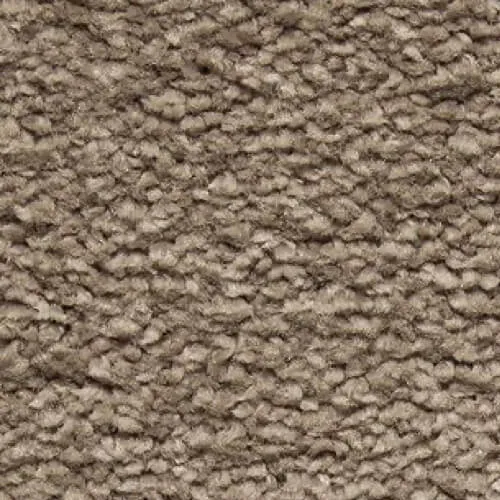
Brown Carpet
Brown carpet is a rich neutral shade that can make the other colors in your room really pop! It's an excellent choice for family rooms and busy households with kids and pets. Brown carpeting can add both character and practicality to your room.
Carpet By Room
Because of its softness and warmth, carpet remains unmatched by any hard-surface flooring solution. It adds comfort and an inviting atmosphere to bedrooms, living rooms, and basements while warming your home in the colder months. It also collects dirt and allergens within its fibers, improving air quality in the home for individuals with allergies.
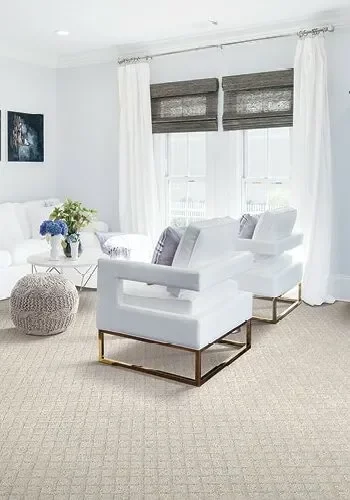
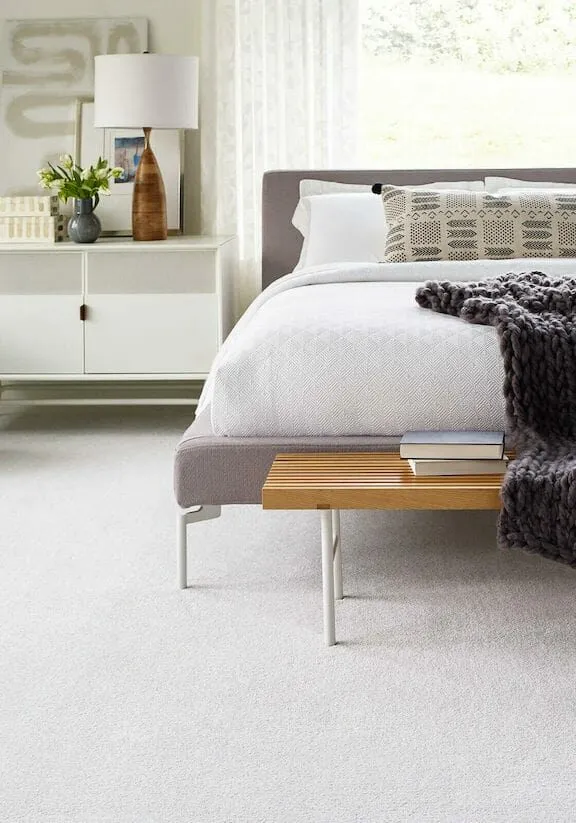
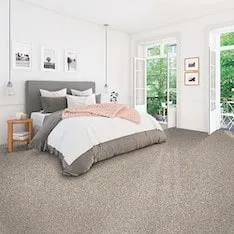
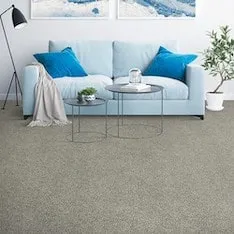
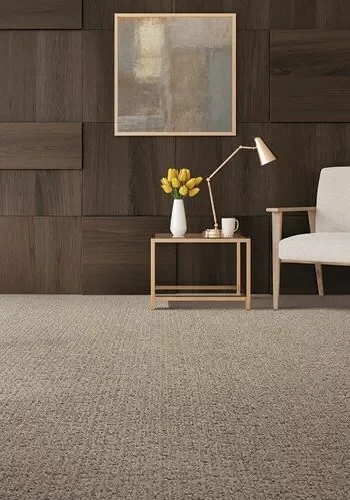
Carpet Styles
When it comes to carpet styles, knowledge is valuable, smart, and desirable. Knowing basic styles can provide you with a firm foundation upon which to begin your shopping journey. Whether you want Berber, frieze, textured, patterned, or more, we have the carpeting perfect for your home. Choosing the ideal carpet style is about knowing the right combination of aesthetics, performance level or material, and budget that meets the needs of your lifestyle.
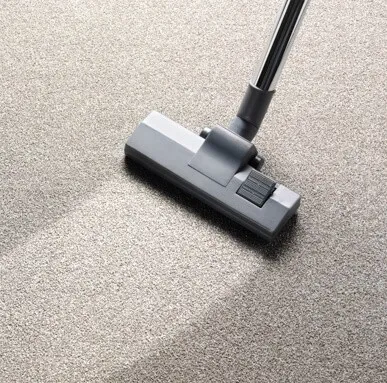
Carpet Care
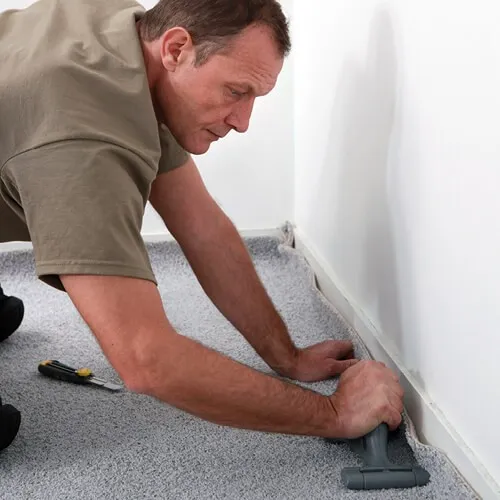
Carpet Installation
Frequently Asked Questions About Carpet
Carpet fibers vary in type and features. Nylon is durable for high-traffic areas, while polyester exudes luxury. Wool offers plushness and vibrant colors. Triexta balances durability with stain resistance, which is ideal for homes with kids or pets. Mohawk's SmartStrand provides a robust, stain-resistant flooring solution. Each fiber has unique advantages, suiting different performance needs.
Carpet construction refers to how a carpet is made and includes cut pile, loop pile, and level cut loop. Cut pile is made by cutting yarn loops, creating a plush feel, perfect for living and bedrooms. Loop pile carpets maintain the yarn's loop structure, offering durability ideal for high-traffic areas. Level cut loop combines cut and looped yarns, providing a textured finish that hides dirt and footprints, making it a versatile choice for various spaces.
Carpet installation is a process that requires precision and specialized tools. We recommend hiring professionals. Installation involves nailing tack strips to the floor to secure the carpet edges. Carpet padding is then laid. The carpet is placed over the padding and stretched using tools like a 'knee kicker' and carpet spreader to attach it to the tack strips along the walls.
For optimal carpet care and maintenance, it is important to vacuum regularly, particularly in high-traffic areas. Clean spots and spills promptly to prevent stains, and invest in an annual professional deep clean. Dirt and debris can wear down carpet fibers over time, leading to a dull appearance. Utilize mats at entryways and remove shoes when walking on the carpet to limit dirt accumulation. These simple steps can significantly prolong the life and beauty of your carpet.
To clean spills on your carpet, act quickly to blot the spill with a clean, dry cloth, working from the outside in to prevent spreading. Never rub, as it can cause the stain to penetrate deeper. Use a manufacturer-approved cleaning solution if necessary. Blot again until dry. For stubborn stains, consider seeking professional carpet cleaning services to ensure proper care and maintenance of your carpet's fibers and colors.
Shop by Brand: Karastan, Dream Weaver, Kane, Masland, Mohawk
Shop by Style: Loop/Berber, Pattern, Texture
Shop by Material: Triexta, Nylon, Polyester, SmartStrand, Wool
Other Resources: Styles Guide, Before You Buy, Installation, Care & Maintenance
Shop by Brand:
Karastan, Dream Weaver, Kane, Masland, Mohawk
Shop by Style:
Shop by Material:
Triexta, Nylon, Polyester, SmartStrand, Wool
Other Resources:
Styles Guide, Before You Buy, Installation, Care & Maintenance
South Florida's largest flooring specialist for over 50 years.
Serving Miami, Pembroke Pines, Davie, Ft. Lauderdale, Coral Springs, Deerfield Beach, West Broward, Doral, W. Kendall
Carpet Store | Flooring Store | Hardwood Flooring Store | Ceramic & Porcelain Tile Floors | Stone Flooring | Laminate Flooring | Inlays, Medallions, Mosaics
Featured Brands | Smartstrand by Mohawk | Mohawk Smartstrand Silk | Mohawk Forever Clean | Mohawk Forever Fresh | Pure Color Polyester & Nylon | Pet Protect | Smartstrand with Dupont Sorona | Scotchguard | dreamweaver | Tuftex | Aladdin | Kane Carpet | Godfrey Hirst | ArmorMax Wood | Armstrong Wood | Engineered Floors | Custom Wholesale Floors | Masters Lumber | Mastercraft | Coretec | Laufen | Roca Tile | MS International (MSI) | US Floors | Porcelanosa | Suncrest | Southland Floors | Mohawk RevWood | Pergo | PureTech by Mohawk | Karastan | Republic | Cali | Stanton | Pet Premier by Mohawk
Additional Markets Served: Key Biscayne, Pinecrest, Cooper City, Miramar, Miami Lakes, Pompano Beach, Dania Beach, North Miami Beach, Miami Beach, Homestead, Key Largo, Marathon, Florida City, Lighthouse Point, Boca Raton, Delray Beach, Miami Springs, Sunrise, Plantation, Weston, Boynton Beach, Hialeah, Palmetto Bay, Hollywood, Opa-locka, Tamarac, University Park, Cutler Bay